Quality Excellence
Centre of Technical Expertise,
Design for Quality Control.
Southern Cable’s production facilities are well equipped with integrated machineries and experienced manpower to ensure that the quality of each cable and wire meets the industry’s standards. Through our efficient production process, we constantly improve our manufacturing capabilities and manage quality control through routine testing, factory acceptance test (FAT) and independent quality control testing facilities.
OUR MANUFACTURING CAPABILITIES
TOTAL
ACRES OF LAND
APPROXIMATELY
TONNES OF
COPPER RODS ANNUALLY
APPROXIMATELY
TONNES OF
ALUMINIUM RODS ANNUALLY
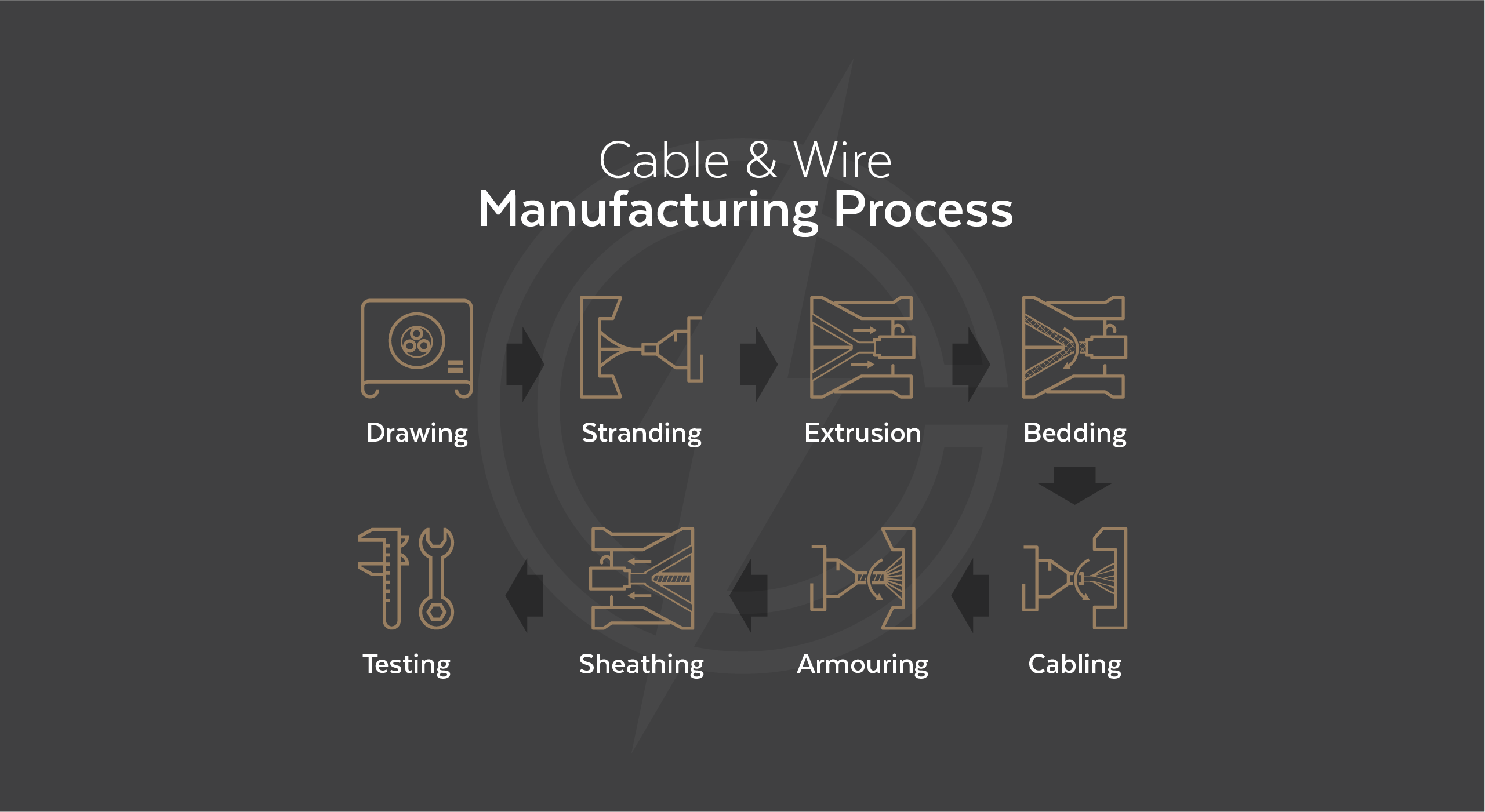
QUALITY CONTROL

Manufacturing Routine Test
Our cables and wires go through an intricate quality-conscious routine test to ensure that all our products comply with the relevant approvals, standards and regulatory requirements. With the extra measures taken, our customers shall be assured to receive up to standard quality products from Southern Cable.
1 Incoming Inspection |
2 In-Process Quality Control |
3 Final Inspection |
4 Delivery |
First Hand Communication
with Product Inspection
Factory Acceptance Test
In addition the above control measures, we also provide factory acceptance test services to our clients before shipping out our products for delivery.
CABLE TESTING & INSPECTION
Manufacturing Testing Capabilities
Throughout production process, the semi-finished product will be inspected and/or tested after each of the process for our cable and wire manufacturing operations. Some of the tests we carry out during in-process quality testing include dimensional, conductor resistance and insulation resistance test.
Before delivering our cables and wires, the final inspection includes of high voltage electrical test, dimensional test, conductor resistance test, insulation resistance test, tensile strength and elongation test. The final inspection process will ensure that our cables and wires meet the customers’ specifications and quality standards before they are sent for packing.